HP Multi Jet Fusion Technology (MJF) In 3D Printing
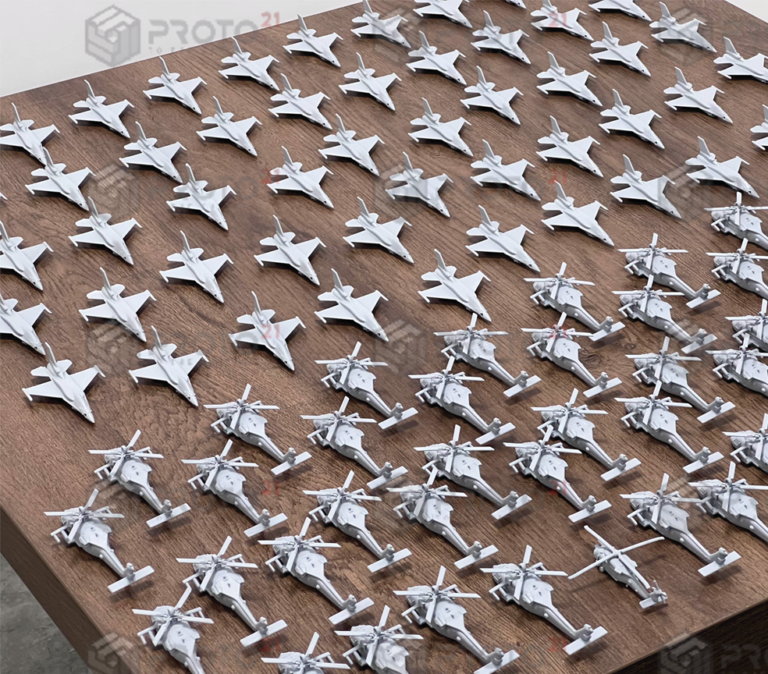
Proto21 3D printing LLC is the first 3D printing service bureau to provide multi jet fusion 3D printed parts into the MENA region. As of today we are capable of manufacturing 130-600 (size dependent) functional PA12 parts isotropic mechanical properties that can be used for detailed prototyping or end-use low volume production. Our industry engagement includes Architecture, Oil and Gas, Robotics, Functional Parts, Visual merchandising, Electronics, Casing and other sectors in Dubai and in the Middle East region.
At Proto21, we have been successful in accomplishing many prestigious projects in no time especially complex models and functional parts that needs to be 3D printed and delivered in few days in the most cost-effective ways using HP MJG technology along with reverse engineering. As we enter industry 4.0, many business is going through a massive transformation and are looking for innovative solutions to expand their freedom of manufacturing flexibility for batch production and that is where the full potential of MJF technology will be used.
What is Multi Jet Fusion (MJF) technology?
Multi Jet Fusion is a powder based 3D printing technology which offers much more possibilities in digital manufacturing for complex and low cost parts. It uses a fine-grained PA12 powder material that allows for ultra-thin layers of 80 microns.
HP Multi Jet Fusion technology gives the freedom to iterate and test various designs and create faster, cheaper, and more lightweight products like gauges, models, sports performance eyewear, helmets, and trophies.
Below are samples of the fresh test prints with the HP MJF 4200 in Proto21.
The PA12 is a strong thermoplastic material well-suited for high-volume functional prototyping and low-volume production applications. It also leads to an exceptionally smooth surface straight out of the printer, hence functional parts and complex thin structures, only need minimal post-production finishing. That means short lead times, ideal for functional prototypes and small series of end-parts.
Why does manufacturing industries prefer MJF over other 3D Printing technologies?
Optimize Productivity
Produce faster and more affordable high quality parts with HP MJF.
Decrease the assembly time and streamline your production processes
Cost Reduction
Produce strong, reliable and functional parts for your exact specification and smoothen your workflow. Optimize production cost with cost-efficient materials that provides optimal output and high reusability at a lower cost per part.
Quality Functional Parts
Thanks to the HP Multi Jet Fusion technology and materials which ensures your printed parts are right for the job – exact, custom, and built to applications
No Supports Required
Multi Jet Fusion technology has the ability to create any unsupported shape with overhangs. As the underlying powder supports the parts, it doesn’t need any generated structures for printing