ABS or PLA
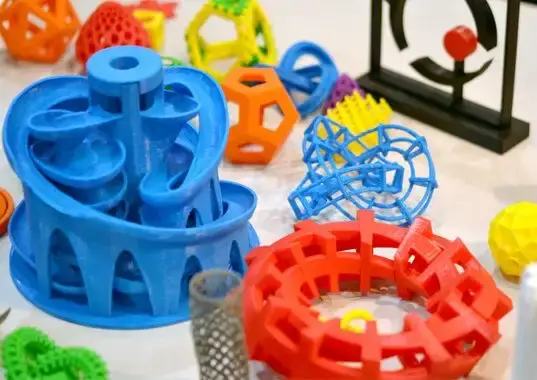
Should you use ABS or PLA in 3D printing?
You can print numerous things through a 3D printer but the most significant factor to consider is using the correct material for your print. There are so many aspects which play a part in making an accurate print which includes the strength, flexibility, and reliability of the printing material.
The two most famous 3D printing materials are ABS and PLA. Both the materials are the type of thermoplastics which allow to shape them when heated and form a particular pattern when there are cool. Most of FDM printers are optimized to print either the ABS or PLA material, but there are some key PLA & ABS differences you need to be aware of.
Introduction to both:
ABS stands for Acrylonitrile Butadiene Styrene, three monomers mixed and linked together. Used in array of industries worldwide, well known for its exceptional mechanical properties. ABS is stronger with higher temperature resistance, but it has bad odour. ABS prints also tend to warp easily when cooled down instantly after printing therefore it is printed in an enclosed chamber. It is not suitable for food contact & in-vivo applications.
PLA stands for Polylactic acid, originally developed as bio-plastic. PLA is derived from plant starches found in potatoes, corn and soy. PLA works for wide range of 3D printing applications because it is so easy to use. It is very rigid and actually quite strong but is very brittle at the same time.
*Sourced from MakeItFrom**Sourced from Optimatter for a test specimen with 100% infill, 0.2mm layer height printed in a linear pattern*** Sourced from Amazon ABS & PLA
Strength:
ABS can withstand more stress and has high structural integrity than PLA. The PLA is mostly used for generic purposes. ABS will distort and bend before breaking whereas PLA more brittle and break under stress. In strength test, PLA withstands more weight before breaking.
Both the ABS and PLA are adequate to 3D print any object due to having similar tensile strengths, but there are some applications which are suitable for one of the two materials.
Surface finish and post-processing:
For both ABS and PLA, the print layers are quite visible after printing. Although PLA tends to have a good finish and gives out better surface quality than ABS. Both the ABS and PLA prints require can be sanded and drilled after printing, but extra care is needed with the PLA print.
ABS has a matte finish, whereas in PLA prints are shinier. In post-processing ABS prints, Acetone can be used to smooth the layers and give it a glossy finish. ABS can be easily sanded and is often machined (for example, drilled) after printing, on other hand PLA post processing requires care.
Heat Resistance:
For high-temperature applications, ABS is more appropriate to use than PLA as it has glass transition temperature of 105°C compared to 60°C. PLA will rapidly sag and deform as the temperature increases and reaches 60°C or more.
Biodegradability:
PLA is steady in normal environmental conditions however it will biodegrade within 50 days in industrial waste and three years in water, ABS, however, is not biodegradable but can be recycled with different industrial processes.
Applications:
ABS due to its strength, thermal stability and flexibility are used to make applications such as plastic toys, electronic housings, and car parts. PLA known for its aesthetic quality is used to manufacture bioplastics, plastic cups and also medical implants.
Melting Point:
ABS primarily has a high melting point. The standard temperature for printing is 230°C while the glass transition temperature is at 105°C.
For PLA it is recommended to operate within 60º C, the material will start to melt at temperatures between 180°C to 220°C. The glass transition temperature for PLA is at 60°C to 65°C.
Print Settings:
For ABS a heated bed is required as the material tends to warp. A person also needs correct ventilation as the fumes from ABS are unpleasant and more toxic than PLA. Careful precautions are required during the melting process as it may cause skin, eye or respiratory irritation.
The PLA is complete opposite when it comes to fumes as PLA exude sweet odor as it uses the sugar-based material. It is more convenient to use and would not warp or crack during printing.
Each of the materials requires a dry location for storage as both are susceptible to moisture.
Accuracy:
Accuracy of the prints primarily depends upon the FDM’s quality and print settings. ABS and PLA filaments can be printed at 60-100 microns layer height. PLA can print complex objects where you can print a vertical overhang up to 68 degrees as compared to only 45 degrees in ABS
Midair connections or bridges also print reliably with PLA particularly with a longer distance between anchor points. But whether you use ABS or PLA, it is recommended to use a raft and make sure your built plate is flat and level.
Conclusion:
Both materials offer different advantages. ABS is known for structural integrity whereas PLA is better known for its aesthetic quality.
PLA is convenient and safer to use but is brittle and break under stress. It is more user friendly and gives a good 3D printing experience. On the other hand, ABS is stronger and more flexible but printing with ABS is not easy to handle.
Whereas, ABS is stronger and more flexible but printing with ABS is not easy to handle.