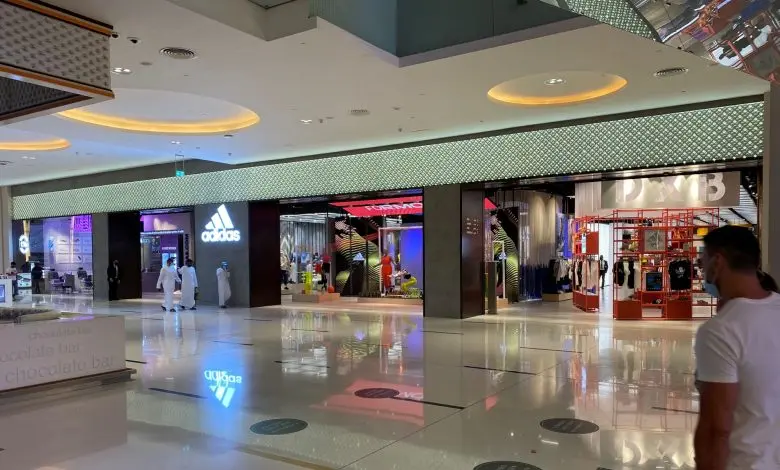
Adidas is a German-based multinational corporation it is the largest sportswear manufacturer in Europe, and is the second-largest sports manufacturing company in the world, after Nike. Adidas is always testing innovations to bring better shoe wear for all sports athletes such as Ricky Rubio, Omar Gonzalez, BJ Upton just to name a few. Even celebrities like Salena Gomez and Kanye West have joined the Adidas bandwagon.
In reality, it is not celebrities that make Adidas a good brand. It is their quality sportswear that makes them shine from their competitors.
Innovation is the second name of Adidas, as they are constantly evolving as a company here are the few examples below on how Adidas has revolutionized the shoe industry:
3D Printed Soles: Many people consider that 3D printers to be a passing craze, while Adidas views 3D printing technology as a creative approach to enhance their line of products. Not only do 3D printed soles look great, but with the help of 3D printing technology, Adidas can manufacture custom soles for a perfect fit.
Sneakers crafted from recycled plastic: Unfortunately, these shoes are not available for the general public, however, the shoes are a good example of Adidas’ inventive use of recycled plastic and care about the environment.
One-piece leather to create a top section of shoes: The shoe top section is usually made with several pieces of materials because it is difficult to acquire the shape for the shoe with just one piece of fabric. Adidas on the other hand has invented stunning shoes by only using one piece of leather that not only looks more elegant but retains the comfort and flexibility that the Adidas brand is famous for.
Proto21 was lucky enough to work with Adidas by 3D printing 1,008 pieces to build the 32-meters long modular façade for the new Adidas Flagship store in Dubai Mall.
The façade is the largest 3D printed model ever created in the Middle East and undoubtedly the largest 3D printed modular item. Every 1008 modular pieces are 200x200x180 mm, the total project took 20,160 hours to complete. A single printer would have taken 28 months to finish the project.
At Proto21, we have 42 Original Prusa FDM printers that completed the project in under three months, including the installation of the modular façade. We used Filamentive’s rPLA material and roughly 450kg of materials were used in the creation of the project. The energy consumed while making the Façade was roughly 2016 kWh. The final result was spectacular, as one would expect from a sportswear business like Adidas, which has been using 3D printing technology and bringing it to the consumers by mass manufacturing midsoles.