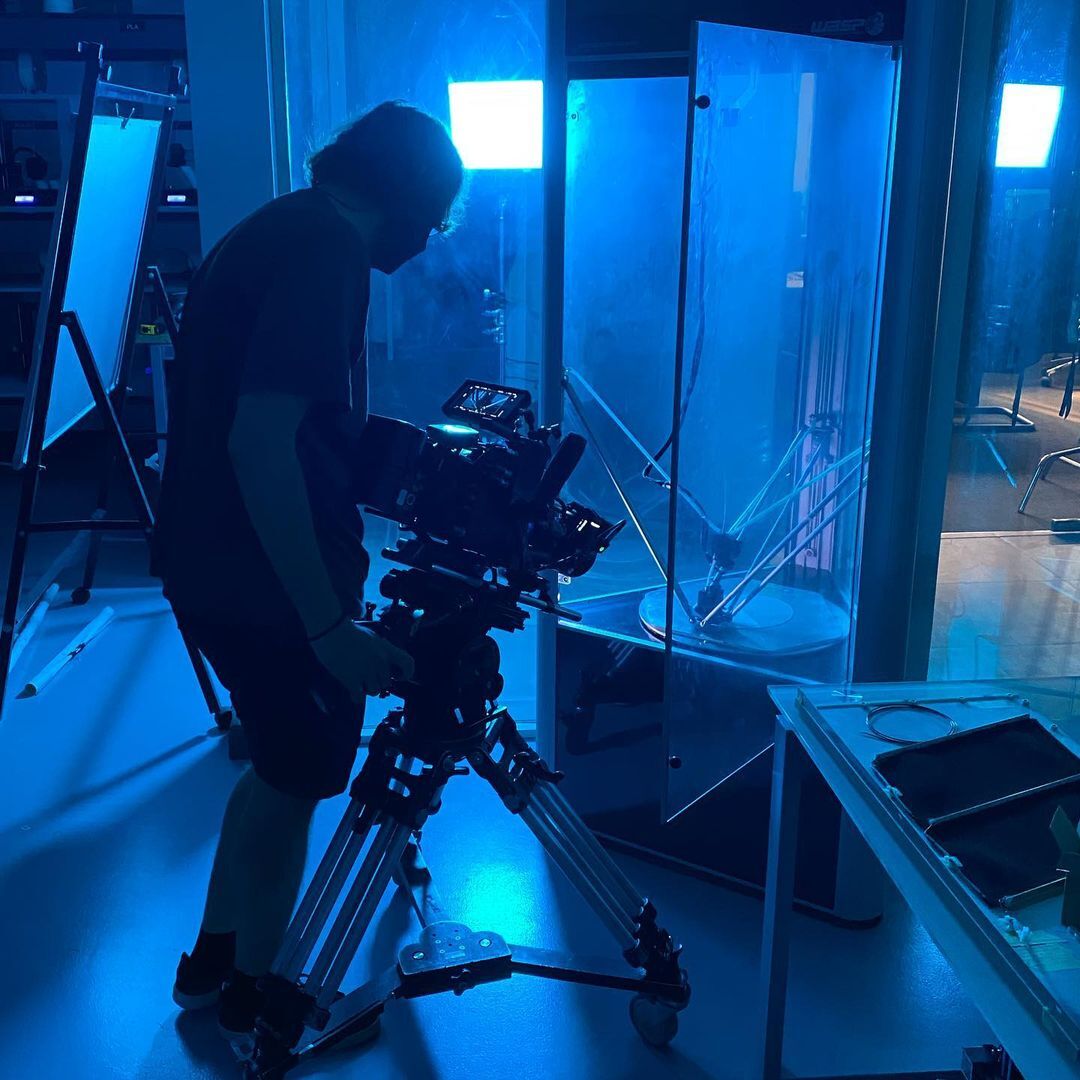
Since the invention of stereolithography in the early ‘80s, three-dimensional printing has ushered in a new era of innovation, disrupting conventional manufacturing practices across various industries.
This technology has unlocked remarkable possibilities, transforming how products are conceptualized, produced and distributed.
Through this revolutionary technology and process, 3D product development has found its way into sectors ranging from aerospace and automotive to healthcare and engineering, allowing for unparalleled levels of customization, speed, reliability and cost-efficiency.
From lightweight aircraft and automotive parts to intricate medical parts and architectural models, the potential of 3D printing knows no bounds, driving industries toward an exciting future of limitless innovation.
Industries Benefiting Greatly From 3D Printing Technology
Below are five industries currently using 3D printing and how this technology is revolutionizing them:
1. Automotive
Ferrari, Bugatti, Lamborghini and Renault are just some of the biggest car companies transformed by 3D printing technology.
Initially, the technology’s primary application in the automotive industry was for producing jigs and fixtures used in the manufacturing process.
However, car companies and other related industries have found more uses for 3D printing. They now use this technology to print prototypes, body kits, cradles engine parts and more.
In general, automotive manufacturers utilize fused deposition modeling (FDM) technology to create plastic parts and selective laser melting (SLM) printing to produce metal parts. Both methods can be used for prototyping.
Some companies also use 3D printers to produce replacement parts for classic cars. With the help of this technology, manufacturers can ensure there are enough pieces for legacy car owners for their spare, repairs and standard maintenance needs.
Some specific examples of how 3D printing is being integrated in the car manufacturing process include:
- Electric vehicle parts
Many companies producing electric vehicles are using 3D printing to produce parts. These include Porsche, which prefers this option since car components made through this technology are lighter, strong and quicker to produce. - Mass production of car parts
For years, Volkswagen has been using 3D printing to mass-produce various car parts, including gear knobs and tailgate letters. - Fully functional cars
3D-printed cars are now also finding their way into the automotive market. For instance, XEV and Polymaker have joined forces to develop Yoyo, a compact electric vehicle, which has three-dimensional printed exteriors and interiors.
2. Aerospace
Since 1989, the aerospace and defense industry has relied on 3D printing for various applications.
Space X, Boeing, Airbus, GE, Safran, GKN and even NASA have found many applications for 3D printing technologies, including the production of tooling, 3D Printed Metal for Engine parts, lightweight aircraft parts and prototyping.
Additionally, since the process produces parts layer by layer, the materials are used only where and when needed. Because of this, there is less waste, particularly when compared to traditional manufacturing methods.
And since the number of components is reduced significantly during the production process, the models created are organically improvised and the assembly time is faster as well.
Lastly, 3D printing produces lightweight parts, making planes and other aircraft lighter. The resulting weight can significantly reduce the airplane’s carbon dioxide emissions, fuel consumption and payload.
Some particular applications of 3D printing in the aviation industry include:
- Engine hot air duct parts
Lufthansa and Premium Aerotec have developed a technology for producing 3D-printed “A-links,” parts that prevent ice buildup in an aircraft engine’s inlet cowl. - Aircraft cabin parts
Emirates Airline is currently working with 3D Systems to produce 3D-printed video monitoring shrouds. The airline also partnered with UUDS to develop air vent grills through 3D printing. - Rockets and satellite parts
According to the BBC, Terran-1, a rocket with 85% 3D-printed materials, was launched in Cape Canaveral, Florida. OreSat0, Oregon’s first satellite, was produced with 3D-printed parts and is already in orbit.
3. Architecture And Construction
3D modeling and printing have been a staple in the construction, architecture and engineering industries for many years now.
This technology allows architects to create plans without resorting to the traditional method of drawing them. With a three-dimensional image of the infrastructure, stakeholders can have an easier time envisioning the final product during pitches.
The 3D visual can also reveal potential issues that 2D plans do not show, allowing the responsible teams to make improvements in real time.
In construction, three-dimensional printing is used to fabricate various types of tools and hardware. It has also found its way into interior design with this technology printing chairs, tables, desks and other features.
3D modeling and printing are ideal solutions for companies and professionals in the architecture and construction industry since it reduces labor time, costs and inefficiencies.
Some projects worth noting in this industry include:
- 3D-printed houses
2021 saw the first three-dimensional home put up for sale in New York. Germany, Netherlands, India, China and other countries are following suit as well. - Commercial buildings
According to the Guinness World Records, The United Arab Emirates is home to the world’s first 3D-printed commercial building, the Dubai Future Foundation (DFF). - Bridges
In 2021, the world’s first 3D-printed stainless steel bridge was completed and opened to the public in Amsterdam.
4. Healthcare
3D modeling and printing have been making waves in the medical and healthcare industry through various applications.
Three-dimensional printing can produce sterile surgical instruments quickly and cost-effectively. By making these medical essentials more available and affordable, 3D printing is contributing to making healthcare supply chains more resilient.
Medical 3D printing is also making breakthroughs in bioprinting, replication and prosthetics. Its specific applications include:
- Bioengineered skin grafts
A team of bioengineers from Columbia University used 3D laser scanners, 3D printing and other technologies to create three-dimensional skin constructs that can be used as “biological clothing” to cover severely burned hands. - Human Body Organs
In 2018, the University of Utah’s biomedical engineers created a method for 3D printing ligaments and tendons using a patient’s stem cells, hydrogel and specialized printer head. - Prosthetic Body parts
A team of scientists from the Israel Institute of Technology has found a way to create an automated production line for 3D printing affordable customized prosthetic hands, arms and legs. - Dental prosthesis
Dentistry has also been transformed by this technology since it can produce better quality dental prostheses, inlays and other implants within a shorter period and at lower costs. In 2012, a 3D-printed lower jaw was fitted to an 83-year-old patient in the Netherlands.
5. Consumer Goods
From toys and electronics to clothing, eyewear, sports equipment and more, manufacturers are harnessing the power of 3D printing to create products that meet evolving trends and consumer demands.
The technology’s application in consumer goods manufacturing starts with product design. Virtual 3D models of products or prototypes can be closely evaluated before they are physically created to identify errors and fix them accordingly.
Moreover, with this technology, product designers and engineers can develop and test versions and perform repetitive testing within a shorter time frame. This solution is also more sustainable than creating numerous samples, which often end up in waste.
These processes allow companies to reduce their time-to-market cycles and offer their products to consumers faster.
3D printing has also helped companies with mass customization. Manufacturers can produce customized products in small batches to cater to the needs of certain sectors faster and in a more cost-efficient manner.
Some of the most popular consumer products with 3D-printed parts include:
- Arevo’s carbon fiber bike
- Chanel’s mascara brush
- Dr. Scholl’s custom insoles
- Specsy’s eyewear
- Gillette’s razor handles
- 3Dvarius’ string violins
As 3D modeling and printing continue to evolve, this technology holds immense potential for further innovation across various industries.
With ongoing developments in materials, printing techniques and scalability, expect even broader adoption and integration of 3D printing into various sectors.
Contact us if you need help bringing your 3D printing projects to life.
Email: info@proto21.ae
WhatsApp: +971 52 104 9913