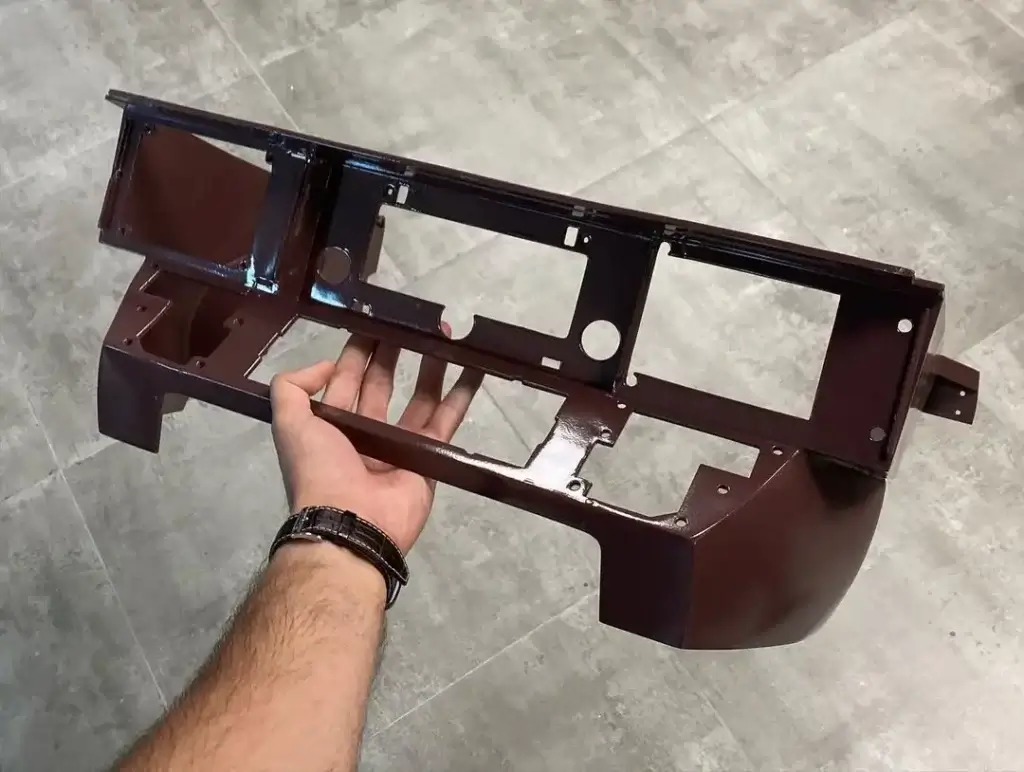
Car manufactures have mostly used 3D printing technologies in the automotive industry to create automotive prototypes to examine the shape and fit over the past few decades. Is it still the case today?
Recently, electric cars and self-driving cars have already become a part of our lives, and are becoming mainstream by many drivers. Automakers are looking for new prospects and materials to catch up with other industries due to the rapid change in the economy and increasingly demanding consumers. In this environment, necessity breeds creativity. The automotive industry was one of the first to use 3D printing technology. It is now possible to print high-quality end-user products like car interior parts.
The first technology used for building car parts was selective laser sintering or binder jetting. This allowed automakers to develop parts that were aesthetically pleasing, however, using that technology has a major drawback as it is not durable and could not be utilized for a long period.
According to engineering.com, there are more robust materials for automotive 3d printing available on the market, such as Fused Filament Fabrication (FFF), which can not only be used for 3d printing prototypes but can also be used by end-used parts and it has become more affordable and mainstream now.
3D printing technology for automotive parts has the potential to revolutionize the industry, it can replace expensive and long lead-time CNC production. 3D printed parts are cheaper and take less time to produce in-house. 3D prototyping can also help to shorten turnaround times at all phases of the production process, and it can provide greater flexibility.
At Proto 21, we are capable of manufacturing customized body kits, functional automotive parts which can be used as end products. We can replicate any automotive parts by reverse engineering with our in-house design capabilities for car restoration projects. Proto21 has created, designed, reversed engineered, and 3D printed numerous parts for the automotive industry, including car dashboards, 3D printed knob controls, rim center logo replacements, 3d printed automotive hood ornaments, and custom screen enclosures for car dashboards.
We can make bespoke body kits and functioning vehicle parts suitable for end-use using in-house design expertise. We have many successful projects in the automotive industry one of which is “Elite Dash” we received an inquiry from a passionate local in UAE who wanted to create a product called “Elite Dash” which is the monitor for upgraded high-performance Nissan Petrol. Proto21 designed a custom model with fir outs of electronics and after prototype approval a low volume production of 25 sets.
In addition to “Dash Elite”, we customized and 3d printed dashboard of classic “Range Rover”, our client reached out to us with the old dashboard part and wanted us to reverse engineer it. We reverse-engineered the dashboard to give it a modern look with an identical fitting to the original piece. We used HP Multi Jet Fusion technology and high-quality European imported paint to give the high-quality finish.
At Proto21, we have a wide range of materials to pick from along with the most advanced 3D printing technologies such as HP Multi Jet Fusion, SLA, Color Jet Printing, and FDM printers. We are the perfect 3d printing company with expert knowledge in automotive and designs. With us, you will always find what you are searching for. To reach us out please contact us via one of the phone numbers provided below or send us your queries through the website, email, or any social media platforms provided below:
Email: info@proto21.a
WhatsApp: +971 52 104 9913
Office: +971 4 235 0902
Follow us on:
Instagram: @proto21.ae
LinkedIn: Proto2
YouTube: Proto21 3D Printing LLC
Advantages of 3D Printing Sculptures
Design Freedom:
Artists today have the freedom to think beyond traditional boundaries by embracing 3D printing as their creative tool. This technology empowers them to explore complex geometries and push the limits of design, unlocking possibilities that were once unimaginable.
Precision and Complexity
3D printing technology presents a significant advantage through its capacity to fabricate highly intricate designs that would be exceptionally challenging through manual methods. Structures characterized by complex geometry, hollow forms, and finely detailed textures can be realized with reduced operational input.
Speed and Efficiency
Traditional sculpting methods are often time-intensive, requiring several weeks or months for completion. Conversely, 3D printing technology substantially accelerates the creation process, enabling artists to rapidly prototype and refine their designs prior to finalizing the printed sculpture.
Cost-Effectiveness
3D printing is a cost-effective alternative to traditional sculpting, which often involves expensive materials and generates a lot of waste. 3D printing minimizes waste by only using the necessary material, applied layer by layer.
Accessibility for Artists
The accessibility of cost-effective desktop 3D printers has democratized the creation of sculptures, enabling independent artists who previously lacked access to expensive sculpting tools to produce impressive works. This technological advancement has provided emerging artists with novel opportunities for exploration.
Challenges and Limitations of 3D Printed Sculpture
Material Constraints
Despite these benefits, limitations persist regarding 3D printing materials. Certain materials exhibit fragility, and the replication of natural textures found in traditional materials such as marble or wood remains a challenge..
Ethical Concerns in Art and Technology
There’s an ongoing debate about whether 3D printed sculptures are "authentic" art. Since artists can replicate designs effortlessly, some argue that it devalues the uniqueness of sculptures.
Technical Learning Curve
Unlike traditional sculpting, 3D printing requires knowledge of digital modeling, software, and printer calibration, making it a steep learning curve for traditional artists.
The Future of 3D Printing in Sculpture
As technology advances, 3D printing will become even more integrated into the art world. Future innovations may include AI-assisted design, self-assembling sculptures, and even bio-printing using organic materials.
Conclusion
3D printing is not replacing traditional sculpture; rather, it is enhancing it. By merging the past with the future, this technology is opening up new creative possibilities while challenging the definition of art itself. Whether you see it as a tool or an art form, one thing is certain, 3D printing is revolutionizing modern sculpture in ways we never imagined.