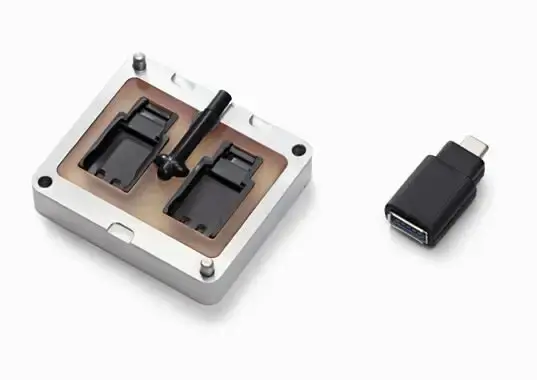
When it comes to the discussion of 3D printing vs. injection printing, which is better for your business? Both technologies have the same objective of manufacturing an object with the addition of the material.
Both injection molding and 3D printing serve the same purpose of rapid development of a design or a prototype. Though, 3D Printing has made life easier. Prototypes that used to cost thousands of dollars and days to produce can now be done overnight at a lower cost.
It has been common word out there that 3D printing is a good alternative to injection molding for rapid prototyping. What percentage of this is true, let’s discuss today.
Unit Production Costs & Order Volume
In terms of 3D printing vs. injection molding costs, the pricing depends on a number of factors. One of the most important involves the number of manufactured parts.
Before creating the final product, you are more likely to design a prototype first. Once you finalize the design, all you need to do is print the object into its final form. This whole cycle has a different approach towards cost when it comes to 3D printing and injection molding.
When it comes to unit prices, the unit costs of manufacturing the parts with 3D printing stay constant irrespective to the increase in the quantity.
When it comes to low volume production 3D printing serves to be the best option in terms of costs. On the other hand, injection molding becomes more practical if there is a large volume of parts that needs to be produced. Injection molding is ideal for rapidly producing very large numbers of identical parts with tight tolerances.
We have designed the following graph to compare the unit costs for both technologies:
Following factors that affect production unit price:
- The number of units produced
- The volume of the 3D printed object
- The complexity of the object’s design
Manufacturing Time
The procedure for manufacturing a single part with injection molding is much faster than the same part done with 3D Printing. This is because 3D printing manufactures the models layer by layer.
On the other hand, during the injection molding process, a mold is filled with liquid plastic material. Depending on the size of the object, this could take a few seconds or minutes.
A print mold can be used for approximately 30 to 100 runs which depends on the material being injected along with the material and the kind of 3D printing technology and material used to produce the mold.
Material requirements of Injection molding process from 3D printed molds are as follows:
- High heat deflection temperature
- High stiffness required to reduce the wear caused by repetitive process
- Accuracy and level of detail
Customization & Iterations
The ability to iterate and maintain agility are essential for any successful product prototyping. Spending a few thousand dollars on a mold which limits any changes for improving our product will most likely slow down our innovation cycle and cost us.
When it comes to customization then 3D printing wins the race here because if offers a virtual format of the object in which you can easily make customization as well as do modification. Making any type of modification or customization in injection molding is impossible.
Complexity
Complexity of the object can drastically affect the manufacturing procedure so it is up to you to opt for the best suitable technology for production. This depends on the model we have in mind and the output that we are expecting.
For hard engineering constraints and tolerances, injection molding wins. On the other hand, 3D Printing is better for complex designs. Every design is possible with 3D Printing due to its layer by layer structure. 3D printing allows you to be creative, giving you a freedom on possibilities on complex designs.
Quality & Finish Of Parts Manufactured.
3D Printed prototypes are not typically finished parts. Due to its layer by layer manufacturing the resolution of prints can’t match with Injection molded parts. They require machining or sanding to remove small rough jagged edges. Moreover, the printed holes must be post processed for better accuracy.
On the other hand, injection molding is an industrial grade manufacturing technology which is made to provide high quality end user products. The final products are detailed with the finishes already applied.
Conclusion
Like injection molding, 3D printing also has its downsides. Today, many 3D printing processes are expensive, slow, and may produce parts that are not up to industry quality or material standards.
It is important to note that each technology has its own pros and cons. Depending upon your budget, time and requirement you can choose either. We at Proto21 can guide you and help you decide what technology is best suited for your project. Contact us now.
Advantages of 3D Printing Sculptures
Design Freedom:
Artists today have the freedom to think beyond traditional boundaries by embracing 3D printing as their creative tool. This technology empowers them to explore complex geometries and push the limits of design, unlocking possibilities that were once unimaginable.
Precision and Complexity
3D printing technology presents a significant advantage through its capacity to fabricate highly intricate designs that would be exceptionally challenging through manual methods. Structures characterized by complex geometry, hollow forms, and finely detailed textures can be realized with reduced operational input.
Speed and Efficiency
Traditional sculpting methods are often time-intensive, requiring several weeks or months for completion. Conversely, 3D printing technology substantially accelerates the creation process, enabling artists to rapidly prototype and refine their designs prior to finalizing the printed sculpture.
Cost-Effectiveness
3D printing is a cost-effective alternative to traditional sculpting, which often involves expensive materials and generates a lot of waste. 3D printing minimizes waste by only using the necessary material, applied layer by layer.
Accessibility for Artists
The accessibility of cost-effective desktop 3D printers has democratized the creation of sculptures, enabling independent artists who previously lacked access to expensive sculpting tools to produce impressive works. This technological advancement has provided emerging artists with novel opportunities for exploration.
Challenges and Limitations of 3D Printed Sculpture
Material Constraints
Despite these benefits, limitations persist regarding 3D printing materials. Certain materials exhibit fragility, and the replication of natural textures found in traditional materials such as marble or wood remains a challenge..
Ethical Concerns in Art and Technology
There’s an ongoing debate about whether 3D printed sculptures are "authentic" art. Since artists can replicate designs effortlessly, some argue that it devalues the uniqueness of sculptures.
Technical Learning Curve
Unlike traditional sculpting, 3D printing requires knowledge of digital modeling, software, and printer calibration, making it a steep learning curve for traditional artists.
The Future of 3D Printing in Sculpture
As technology advances, 3D printing will become even more integrated into the art world. Future innovations may include AI-assisted design, self-assembling sculptures, and even bio-printing using organic materials.
Conclusion
3D printing is not replacing traditional sculpture; rather, it is enhancing it. By merging the past with the future, this technology is opening up new creative possibilities while challenging the definition of art itself. Whether you see it as a tool or an art form, one thing is certain, 3D printing is revolutionizing modern sculpture in ways we never imagined.